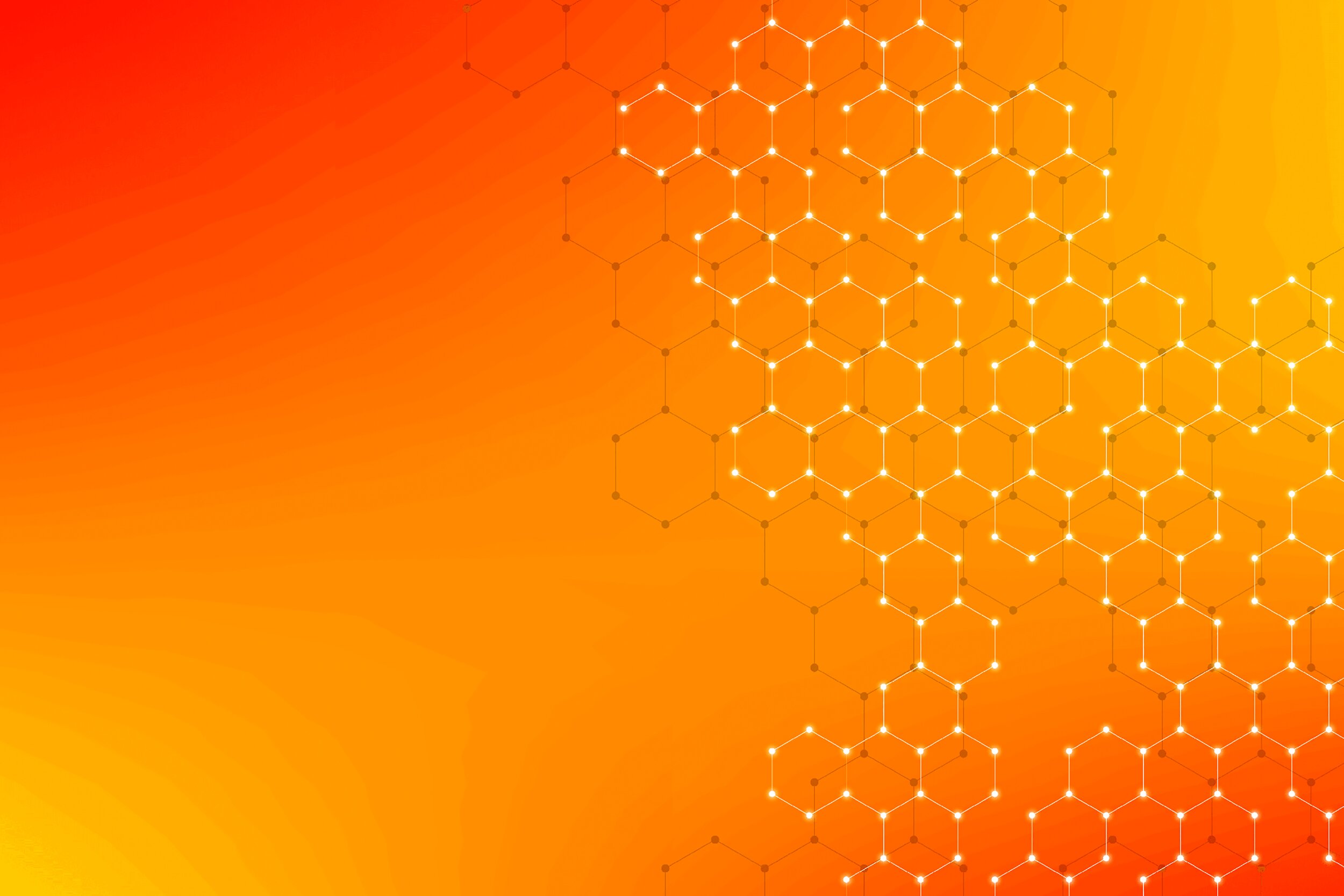
Honeycomb for
Manufacturing
Modern manufacturing is about more than assembly lines or even a finished product. Companies are focusing on becoming more efficient in every aspect of production.
More than any other approach, data and the analytics used to understand it is the way forward.
Not only does such information give an insight into the current status of your business, it can help you understand the bigger picture behind it. This might mean understanding human productivity, such as what impact the current levels of output have on motivation and happiness. It could be used to gauge the performance of your manufacturing machinery, from the largest pieces of technology, all the way down to a single computer chip or sensor.
In general, data analytics help manufacturers go from making predictions about their performance to actually being prescriptive and being able to make changes on the fly that accurately represent the needs of their staff, stakeholders, and customers. It’s all about getting from a simple display of data to being able to leverage that data. That kind of power helps to reduce costs and increase efficiencies in the supply change.
In order to do this, however, companies need a way to link and centralize all their data in one location. This is exactly why we created Honeycomb. With our data lake technology, manufacturing companies are able to harness the competitive edge of these insights to make their business more streamlined and focused on forward progress. Let’s take a look at six ways that Honeycomb can help manufacturing companies become better, sharper, and more agile in doing right by their product and customers.
Agile Development by Expert Teams
Our data analytics solution is the result of countless hours, late nights, and coding sprints by Moser’s talented team of developers. But the process of fitting Honeycomb for use by manufacturers doesn’t stop there. In fact, it can’t stop there. That’s why we use an agile development process that allows us to continuously update, improve, and create a data analytics process that works for your company for the long term.
Every manufacturer is different; whether it’s their industry needs, type of materials used, or even just the company’s ethos or guiding principles. For example, SMC Corporation is using our Honeycomb solution in their own, personal way. This is true even at their North American headquarters located in Noblesville, Indiana, as explained by product manager Stephanie Costello.
“We’re a global pneumatics manufacturer. We have many, very large transactions, and those come in from a lot of places, like a marketing website, our company website, and our engineering team. All of those need to be included in a data solution.”
So, Moser used all of these unique aspects of SMC to customize a solution that united these different components. And, as new pieces are added to SMC’s customer approach, our agile teams can continue to fit those together, like a continuously growing jigsaw puzzle. Regardless of how many new pieces there are, we never lose the bigger picture.
Automation and Modernization Best Practices
The customization process of integrating Honeycomb as a viable data solution is important. But even before then, we need to ensure that the automation process is being form fit to your manufacturing company’s needs.
Because of the unique design of each company, so too are the places your data is already stored. Once we get started, Moser’s engineering team puts its focus on building and integrating the secure frameworks for collecting data from any of your company’s silos. To ensure all of this is handled correctly, we deploy a personal Product Owner to coordinate the entire process of digging deep into your organization’s strategy, all the way from the manufacturing facilities, to your marketing and sales teams, to the logistics team shipping these products out to customers.
The Product Owner will ask questions and listen intently to your answers to best understand not only your bottlenecks, but where you’ve traditionally done well in the past. For example, part of SMC’s data automation revolves around the need to provide pricing information for each of their different distribution channels.
Our clients rely on us for custom part ordering.
However, they also need pricing information; we currently have four different levels of distributors, all of whom have their own pricing structures and non-corresponding part numbers. Currently, we generate a full file of 750,000 parts once every two weeks. That’s a long holdup for anyone who needs pricing information, especially if it’s for a rush job.
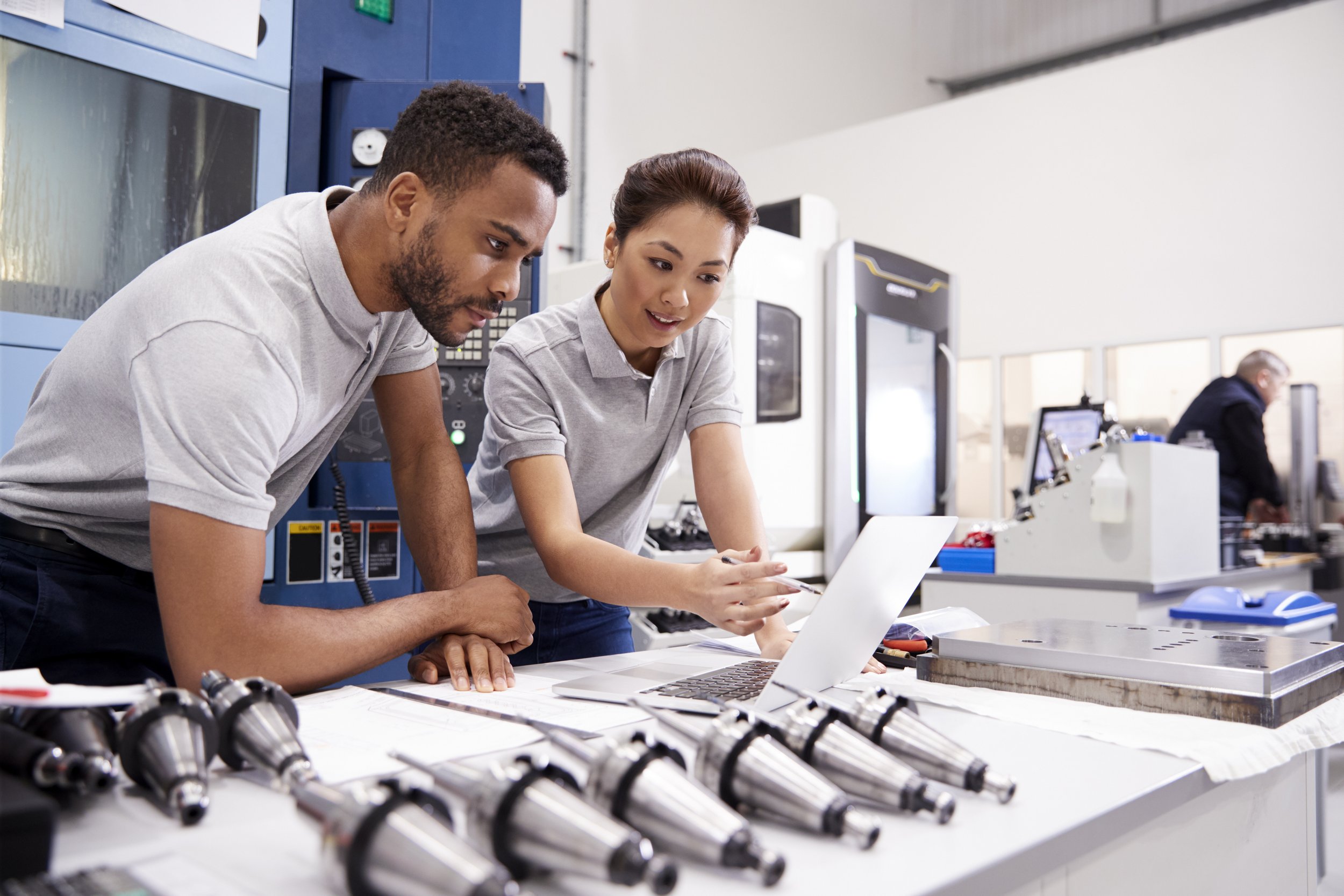
Data Integration
The entire point of data lake solutions is to centralize manufacturing, shipping, and customer data in one easy-to-use location. As a business grows, it’s extremely easy for silos to unintentionally develop. Each entity may have its own way of storing and retrieving data; it’s ours and Honeycomb’s job to organize and unite these sources of information.
“We have a lot of applications for customers and non-customers to utilize. So we can look at analytics and understand who is coming to our website, what they’re looking at, what they are doing,” said Costello. “That’s great data that currently we’re not able to link up with sales, invoicing history, and where it’s coming from. We need to incorporate that into our CRM.”
This is exactly what Honeycomb can do for your manufacturing company. When these data sources are filtered into one location, your business team can do more with the information. Suddenly, you’re not just storing data; you’re harnessing power by illustrating correlations, cross-referencing information, and generally getting a clearer picture of exactly what is working right at your manufacturing company.
Data Platforms
Whether you’ve used data lake solutions before or not, analyzing that information takes practice and guidance. Real-time analysis requires the right types of platforms that serve your manufacturing needs.
By working closely with your staff, we’re able to help you harness all the data to do more with it. Like all parts of the Honeycomb product process, this is based entirely on your individual needs. Costello explained how the Honeycomb team was able to create platforms and usages that were most beneficial to their unique process.
“During the setup, they have had to understand our system to help us migrate info into Honeycomb. The entire time, they have been great,” she said. “Sometimes during a meeting we’ll work through different tables and scripts to help them, and they’re always intently listening and asking questions. They’re very hands on, very transparent, and very willing to share information.”
Though SMC is using Honeycomb for a variety of efficiencies, we understood quickly that the most important one was to unite customer data for feedback on customized orders.
That’s why we built the platform to address that issue, “With Honeycomb we can find all the info we need and customize it with each customer and just give them the info they want for their account.”
In order to keep costs low and computing power high, Honeycomb utilizes the power of cloud technology. This approach allows developers and your company to see real-time data integration in one central location. It also means instant scalability. As your business grows, the needs for your data lake analytics may change. On traditional legacy systems, this would mean standing up new physical servers to increase memory, or programming entirely new software that’s redesigned for your needs. But with the power of the cloud, it’s easy and affordable to spin together virtual servers, expand and make more memory, and add new features without breaking a sweat.
But in addition to these benefits, the cloud solution aspect means increased security for your data and your customers. Data is immediately and routinely backed-up, meaning that it’s easily recoverable if lost due to a breach, crash, or any other disaster that could befall your system. This benefits manufacturers like SMC in two ways: by saving costs, and by demonstrating your reliability to clients.
“Our product creation process is all about customer satisfaction and customization. When it comes to orders, now it’s just a standard file that doesn’t allow us to show the changes made between orders. We’d like to just let them know what changed,
but it requires so much personal data. By using cloud solutions with the Honeycomb product, it keeps us safe as well as the information stored on our servers.”
Cloud Solutions
50% of manufacturers experienced a data breach in 2018, and 11% of those were considered “major breaches.”
Data Exploration and Visualization
Overall, the benefit and point of Honeycomb is to interpret big data and provide your team with easy-to-use and easy-to-digest information. This isn’t done with confusing spreadsheets or inscrutable statistics; we have created a solution that can visualize and display data findings. These visualizations allow anyone on your team to see what customers need and how well your manufacturing process is working to accomplish those tasks.
“We can’t follow a full customer journey through our website to sales,” they said. “Honeycomb and its visualizations of our data just means it’ll be easier. We should be able to uncover a lot more trends and patterns that correlate that we don’t even notice right now.”
Honeycomb uses simple dashboards that provide control over data exploration, and the ability to generate new visualizations that fit your manufacturing and logistics strategies. Even if you’re using third-parties for things like shipping or order fulfillment, those teams can also greatly benefit from the data exploration and visualization capabilities.
“We have four different levels of distributors with different pricing structures. They all have their own part number compared to ours. So, customers want to see the cross reference between our part number and theirs, so it’s all clear. They want to see the discounts they get, and how it differentiates for things like volume. Honeycomb is helping us provide accurate pricing in these different formats.”
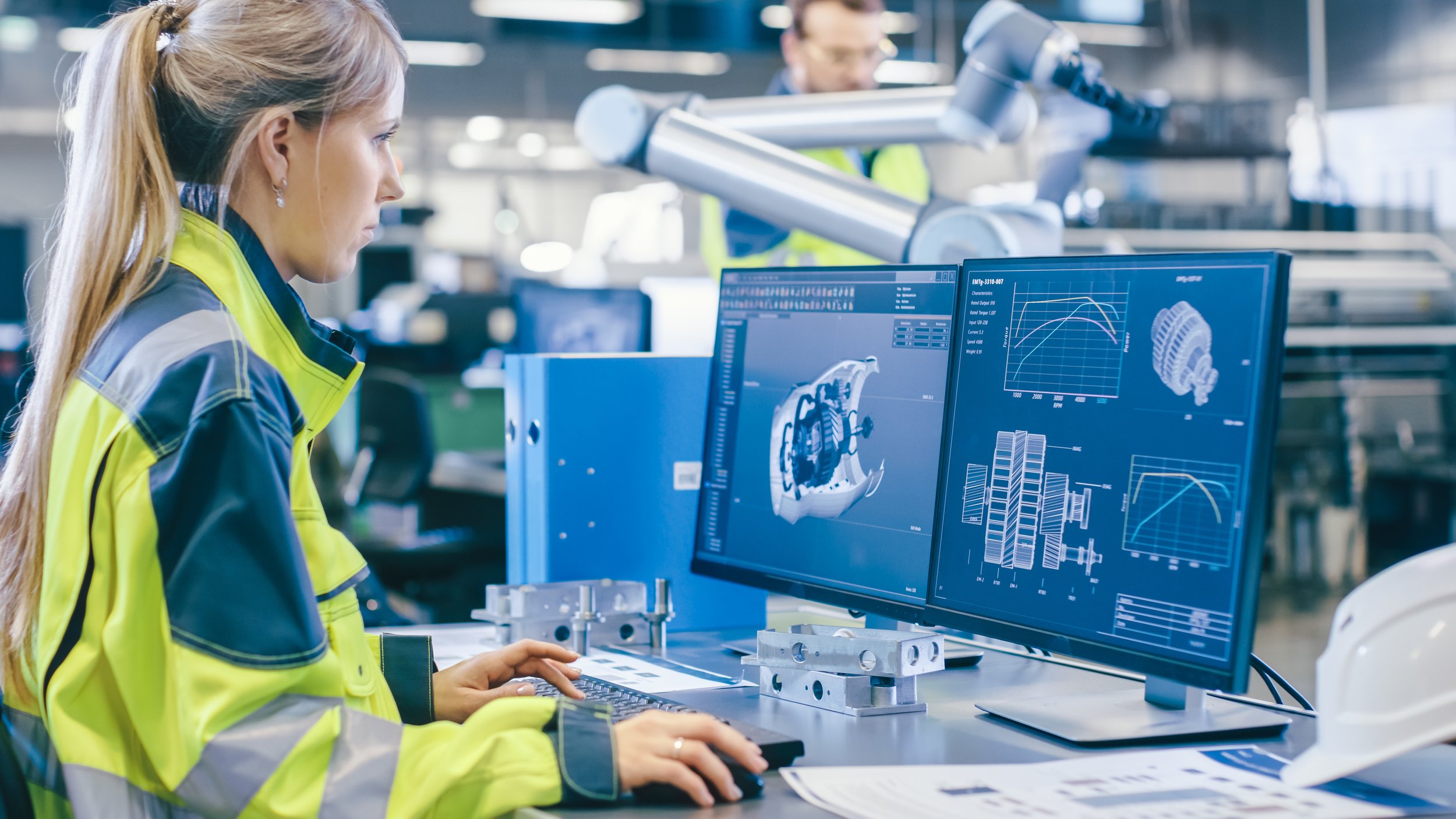
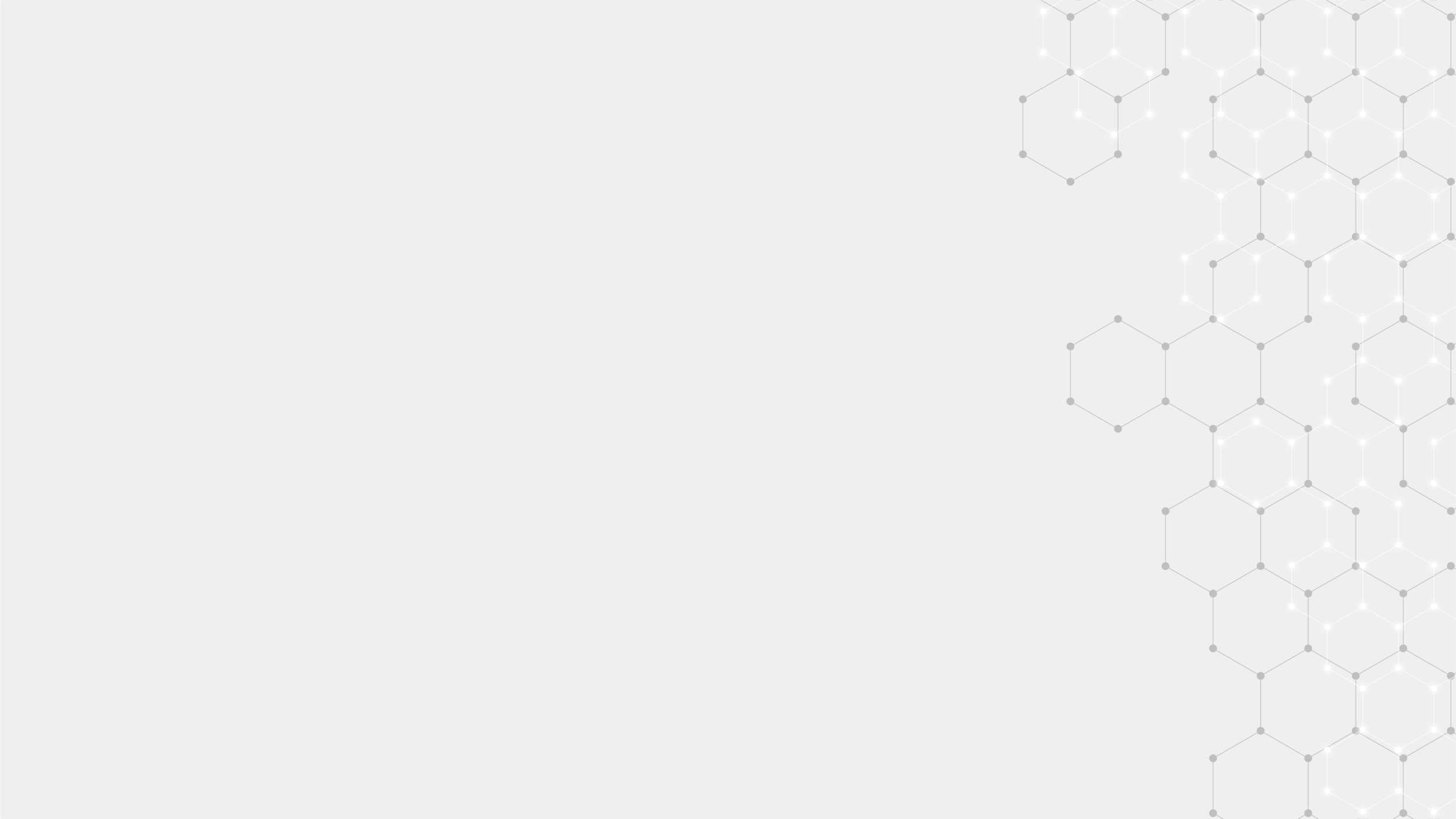
Transforming Manufacturing with the Power of Data
“Working with Moser has been awesome. They’re always looking for new ways that we can implement the product. They’re listening to our conversations and looking for ways we can utilize Honeycomb. It’s been a transformative experience.”
This is the exact kind of feedback we thrive on. We have built Honeycomb to be an industry agnostic solution, so when a company or organization tells us that we’ve made their lives easier, it means the world to us. If you’re interested in taking advantage of your company’s data, we know that Honeycomb could be the missing piece in your process. Contact us today so we can learn more about your company and explain exactly how we can help you achieve more with digital transformation.